3D Drucker für die Modellbahn
Noch vor
wenigen Jahren waren 3D-Drucker nur im professionellen Bereich angesiedelt.
Grund hierfür waren die enorm hohen Kosten.
Mittlerweile sind nun viele Modelle auch für den Privatgebrauch
erschwinglich. Die Preise bewegen sich dabei zwischen rund 350 und 3500 €
(Stand November 2014).
Was können die Geräte?
3D Drucker
sind - wie der Name bereits sagt - in der Lage, dreidimensionale Objekte
herzustellen. Bei den erschwinglichen Druckern wird dabei ein
Kunststoffdraht erhitzt und durch eine Düse Lage um Lage ein Objekt
aufgebaut. Dazu wird die Platte, auf welchem das Objekt entsteht, in der X-
und Y-Achse bewegt. Bei jeder neuen Lage bewegt sich die Düse etwas nach
oben (Z-Achse).
Modelle
Mittlerweile
sind viele ganz unterschiedliche Modelle für den Privatgebrauch erhältlich. Die meisten werden als
Fertigmodelle angeboten, wie beispielsweite der MakerBot.
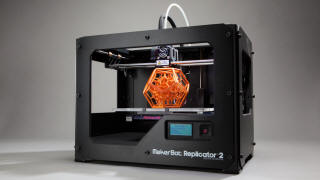
Foto: MakerBot
Einer der
derzeit günstigsten 3D Drucker ist der
Velleman K8200 (Stand:
Ende 2014). Dieser
wird als Bausatz geliefert.
Und so sieht das fertige Modell aus. Im Gegensatz zum MakerBot ist dieser
Drucker als offene Rahmenbauweise aufgebaut.
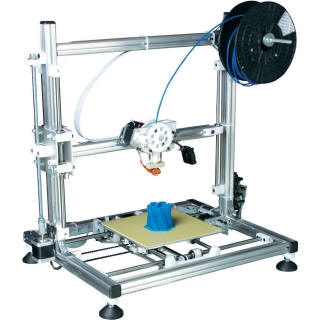
Foto: Velleman
Aufbau des Druckers
Die meisten 3D-Drucker sind vom
Prinzip her ähnlich
aufgebaut. Beim Velleman Drucker wird das Druckbett in X- und Y-Richtung
bewegt. Die Z-Achse wird mittels einer M8 Gewindestange bewegt. Die
Druckdüse mit dem Extruder ist fest auf dem Querbalken der Z-Achse
angebracht.
Hier sind die wesentlichen Teile
des Druckers bezeichnet:
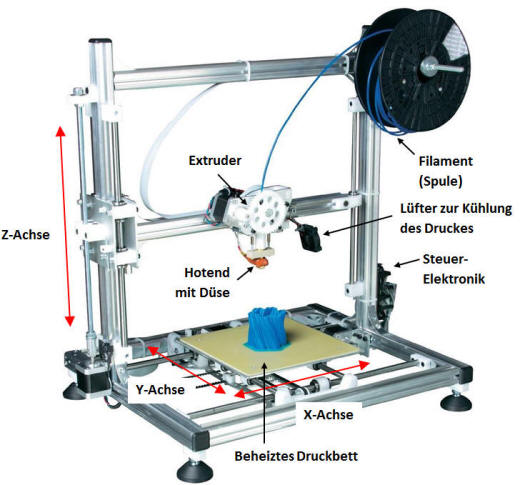
Zum Druckbeginn befindet sich die
Düse knapp über dem Druckbett. Das Druckbett wird je nach verwendetem
Material (PLA, ABS, Nylon) beheizt, bei PLA beispielsweise auf 50...60°C.
Damit haftet das Objekt besser und kühlt nicht zu schnell aus, was zum
verziehen des Objektes führen könnte.
Über die X- und Y-Achse wird das Druckbett bewegt. Gleichzeitig drückt
der Extruder das runde Filament durch die bei PLA auf 190°C beheizte Düse (Hotend).
Bei ABS beträgt die Temperatur circa 230°C.
Ist die erste Lage gedruckt, welche je nach Anwendung im Bereich von 0.1
bis 0.35mm Dicke liegt, bewegt sich die Z-Achse um eine Lagendicke nach
oben. Nun wird die zweite Lage gedruckt, und so fort.
Der Lüfter kühlt dabei das gedruckte Filament (den Kunststoff) ab, was
vor allem bei "Überhängen" von entscheidender Bedeutung ist.
Der K8200 Bausatz
Der Bausatz kommt in sehr vielen
Einzelteilen daher, welche in einzelnen Säckchen - für jeden Bauschritt -
abgepackt sind.
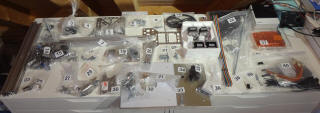 |
Ganz viele einzelne Beutel mit vielen Kleinteilen: so
präsentiert sich der 3D Drucker beim auspacken. |
Zusammenbau
Die 765 seitige Bauanleitung muss
von der Hersteller-Webseite herunter geladen werden. Die Anleitung ist sehr
detailliert, obwohl bei der Übersetzung ins Deutsche ein paar kleine Fehler
vorhanden sind. So heissen Muttern in der Anleitung Schrauben.
Der Zusammenbau gelingt ohne grössere Probleme, sofern das richtige Werkzeug
vorhanden ist. Gute Erfahrung beim Löten ist angesagt, um die vielen
Kabelverbindungen herzustellen. Hier hätte ich eine andere Vorgehensweise
empfohlen.
Nach dem Zusammenbau des K8200 - wofür man
rund 20 Stunden einkalkulieren sollte - geht es weiter mit der mechanischen
und elektrischen Justierung der Maschine. Dies ist nicht ganz einfach, muss
aber sehr sorgfältig durchgeführt werden. Für die mechanische Einstellung
ist eine Fühlerlehre empfehlenswert. Die elektrische Kalibrierung erfordert
ein präzises Voltmeter.
Teile aufbereiten und Drucken
Etwas unklar ist die Anleitung
hinsichtlich der benötigten Software. Das Konzept ist für Laien nicht auf
den ersten Blick offensichtlich. Deshalb gehe ich hier etwas näher darauf ein.
Damit ein Bauteil gedruckt werden
kann, sind mehrere Computerprogramme notwendig.
Ganz grob kann man es so darstellen:
Bauteil
zeichnen/erstellen
Hierzu wird ein 3D CAD Programm benötigt.
Ein mögliches Programm ist
FreeCAD.
Ein anderes ist
AutoDesk
123D Design, welches ebenfalls kostenlos ist.
Nach dem erstellen des Objektes muss dieses als Mesh Format (.stl)
exportiert werden.
Diese beiden Programme können kostenlos heruntergeladen werden.
|
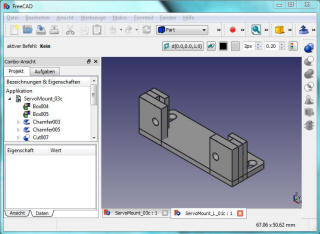 |
Bauteil für den Drucker
aufbereiten
Das erstellte 3D Objekt muss nun in einzelne "Scheiben" geschnitten
werden. Jede Scheibe entspricht dabei eine zu druckende Schicht.
Hierfür wird das Programm
Slic3r oder ein
anderes Slicer Programm benötigt.
Hier wird die .stl Datei importiert.
Das Programm erzeugt aus der stl Datei die einzelnen
Befehle für den spezifischen 3D Drucker, wie Steuerung der Temperatur,
Geschwindigkeit und alle Bewegungen der X/Y/Z Achsen sowie des
Extruders.
Dazu muss dieses Programm die Eigenschaften des Drucker kennen. Die
Hersteller liefern hierzu für viele Drucker eine Konfigurations-Datei (.ini) welche
importiert werden kann.
Die Drucker-Befehle werden in eine Datei
als Format geschrieben, welche als GCode von CNC
Maschinen her bekannt ist.
Neben Slic3r hat sich vor allem auch
Cura
bewährt. Dieses bietet in der aktuellen Version (Stand Nov. 14) die
besten Ergebnisse. |
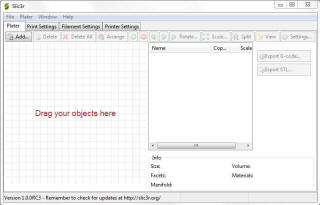 |
Drucker-Steuerung
Nun muss der Drucker auch noch angesteuert werden, d.h. die Motoren
müssen sich bewegen, das Hot-End und Druckbett aufgeheizt werden usw.
Dazu dient das Programm
RepetierHost.
Dieses Programm steuert alle Motoren entsprechend den Befehlen im
GCode.
Dieses Programm steuert also den Drucker direkt an
(meist über USB). Dabei kann der Drucker über diese Software auch
manuell gesteuert werden. So können die Motoren bewegt werden, der
Extruder (das ist die Düse bei welchem der flüssige Kunststoff
austritt) aufgeheizt oder der Lüfter eingeschaltet werden.
Wenn Cura verwendet wird, kann das Teil direkt ausgedruckt werden.
Cura kann sowohl die Datei "slicen" wie auch den Drucker ansteuern. |
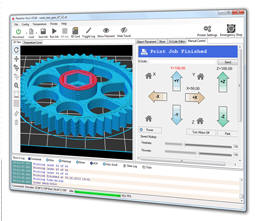 |
Und wie sieht das Ergebnis aus?
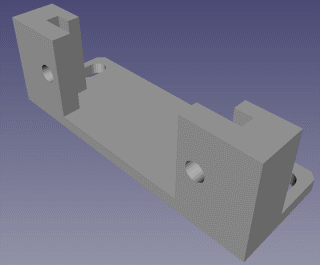 |
So sieht ein in FreeCAD gezeichnetes Teil aus.
Eine Servo-Halterung für Mini-Servos. |
Und das macht der 3D Drucker
daraus.
Hier mit montiertem Servo. |
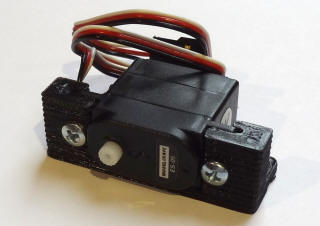 |
Probleme
Der 3D Drucker K8200 von Velleman hat
einige Probleme. Es sollte einiges nachbearbeitet werden, was dank der
offenen Bauform aber keine grösseren Schwierigkeiten bereitet.
Folgende Änderungen verbessern die Druckereigenschaften massgeblich:
 | Bett: dieses ist als Leiterplatte auf einem
geschnittenen Alu Blech aufgeschraubt. Problem dabei: es ist nicht exakt
plan. Eine Glasscheibe oder (von einigen empfohlen) ein IKEA Wandspiegel
aufgeklebt ist absolut plan. |
 | X- und Y-Achse: diese haben zu viel Spiel und
lassen sich kaum einstellen. Eine Vorrichtung zum Spannen des
Zahnriemens fehlt und sollte nachträglich eingebaut werden. |
 | Montage der Motoren: Hier werden Winkel aus
abgekantetem Alu Blech geliefert. Diese sind leider nicht genau 90°. Aus
diesem Grund läuft der Zahnriemen auch nicht mittig im Zahnrad. Abhilfe:
eigene Winkel selber ausdrucken (können im Internet herunter geladen
werden). |
 | Extruder liefert kein Kunststoff: In meinem
Fall hat der Extruder kein Kunststoff ausgegeben, obwohl - von Hand
bewegt - der Kunststoff aus der Düse ausgetreten ist. Das Problem lag an
der Einstellung des Motortreibers: die von Velleman genannten 425 mV
Referenzspannung reichten nicht, der Motor hatte zu wenig Kraft und
konnte das Material nicht transportieren. Eine Erhöhung auf 550 mV
brachte den gewünschten Erfolg. |
Bisher durchgeführte Verbesserungen
Im Bild des
Servo-Halters oben erkennt man deutlich die "Rillen" bei den einzelnen
Schichten. Um diese zu verringern habe ich folgende Änderungen an meinem
Drucker vorgenommen:
Neue Motorhalterung für die X-Achse
Diese war
ursprünglich ein einfacher, aus abgekantetem Alublech hergestellter
Aluwinkel. Leider betrug der Winkel nicht exakt 90°, weshalb der Zahnriemen
nicht mittig im Antriebsrad lag. Hier habe ich einen neuen Montagewinkel auf
dem 3D-Drucker ausgedruckt.
Zudem habe ich den Zahnriemen und das Antriebsrad auf GT2 gewechselt.
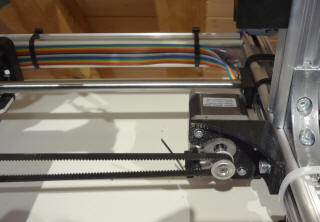 |
Neue Halterung für den X Motor, neuer
Zahnriemen (GT2) und Pulley. Daneben wurde der Zahnriemen mit einem
Spanner versehen. |
Noch besser: Zwei Riemen
Da der neue Riemen der X-Achse bei
hohen Geschwindigkeiten zum Vibrieren neigte, habe ich mittlerweile die
Konstruktion verfeinert. Jetzt wird die X-Achse über zwei GT2 Riemen bewegt:
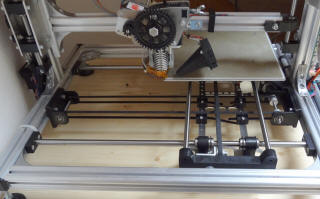 |
Die neue Konstruktion mit zwei Zahnriemen für die X-Achse. |
Verbesserungen an der Z-Achse
Trotz der Änderungen an der X-Achse wurde das Druckergebnis nur leicht
besser. Das Problem lag bei der Z-Achse. Hier war die Motorwelle starr mit
der M8 Gewindestange verbunden, welche für die Z-Bewegung zuständig ist. Da
auch hier die Halterung des Motors und die Kupplung nicht sehr präzis
ausgeführt waren, hat eine Drehung der Z-Achsenwelle jeweils den Extruder
leicht verschoben.
Abhilfe war eine neue Halterung für den Z-Achsen-Motor sowie eine flexible
Kupplung.
Erst die flexible
Kupplung der Motorwelle (5mm) zur M8 Gewindestange (8mm) hat das
Druckergebnis markant verbessert.
Der Motor der Z-Achse wurde ebenfalls mit einer neuen
(ausgedruckten) Halterung montiert.
Daneben wurde auch eine neue Halterung für die Kalibrierung der
Z-Achse ausgedruckt und montiert. |
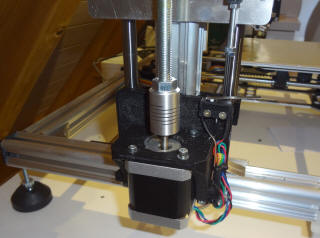 |
Mittlerweile hat der Hersteller
(Velleman) das Problem mit der Z-Achse erkannt und bietet unter der
Artikelnummer K8204 einen Umbausatz an. Darin enthalten ist eine
Trapezspindel mit entsprechender Mutter, welche die M8 Gewindestange
ersetzt, sowie eine flexible Kupplung.
Ich habe diesen Umbausatz bei meinem Drucker montiert und konnte damit das
Druckergebnis nochmals deutlich verbessern.
Verbesserung des Spulenhalters
Die Filament-Spule wird im
Originalzustand des Druckers einfach auf eine M6 Gewindestange gelegt. Je
nach Ausführung der Spule dreht sie sich mal besser, mal schlechter, auf
jeden Fall liegt eine mechanische Spannung auf dem Kunststoffdraht.
Ich habe konische Aufnahmen
konstruiert, welche innen mit einem Kugellager versehen sind. Mit einem
Handrad mit integrierter M6 Mutter werden die Aufnahmen mit der Spule
dazwischen festgehalten.
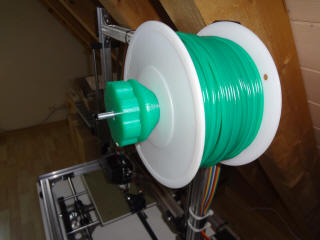 |
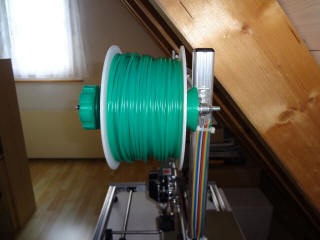 |
Mit diesen Teilen dreht die
Spule sehr leicht, dank den beiden Kugellagern, welche sich in den
konischen Aufnahmen befinden. Die Teile wurden in FreeCAD gezeichnet
und auf diesem Drucker ausgedruckt. Dank der konischen Form können
alle handelsüblichen Rollen verwendet werden. |
Heizbett mit höherer Spannung betreiben
Ein Kritikpunkt am K8200 ist die
lange Aufwärmzeit des Heizbettes (das ist die Platte, worauf gedruckt wird).
Beim Material PLA sollte diese auf rund 50 bis 60°C geheizt werden, damit
das gedruckte Objekt gut haftet. Bei ABS muss die Heizplatte noch einiges
wärmer sein.
Bis die erforderliche Temperatur erreicht wird, kann es im Originalzustand
gut 20 Minuten (60°C) dauern, eine viel höhere Temperatur ist kaum möglich (max
rund 70°C bei 25°C Umgebungstemperatur).
Ich habe hierfür eine separate
Stromversorgung installiert, indem ich ein altes Laptop-Netzteil mit 19.5V
Ausgangsspannung über ein MOSFET an das Heizbett angeschlossen habe. Das
Signal zum Ein- und Ausschalten wird vom Heizbettausgang über einen
Optokoppler geführt.
Damit wird die Leistung gegenüber
dem Velleman Netzteil (15VDC) erheblich erhöht. Kurze Aufwärmzeiten sind nun
möglich. Zudem können weit höhere Temperaturen von bis zu 90°C erreicht
werden, was auch für ABS ausreicht.
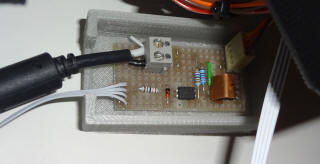 |
Mit dieser kleinen
Zusatzschaltung wird ein zweites Netzteil mit höherer Spannung an
das Heizbett angeschlossen.
Der Betrieb ist problemlos, Rückwirkungen auf die Originalschaltung
sind durch den Einsatz des Optokopplers ausgeschlossen. |
In der Zwischenzeit habe ich das
19.5VDC Notebook Netzteil durch ein 24VDC Netzteil mit 90VA ersetzt, was
nochmals eine schnellere Aufwärmzeit ermöglicht. Auch die maximal mögliche
Temperatur hat sich erhöht. Ich habe das Heizbett damit schon auf
Temperaturen über 110°C erhitzt.
Mit dem 24VDC Netzteil wird die Leistung am Druckbett gegenüber der
Originalausführung rund verdreifacht. Das 24VDC Netzteil muss
dementsprechend eine Leistung von mindestens 90VA liefern können, besser
wären 100VA.
Und so sieht das Schema dazu aus:
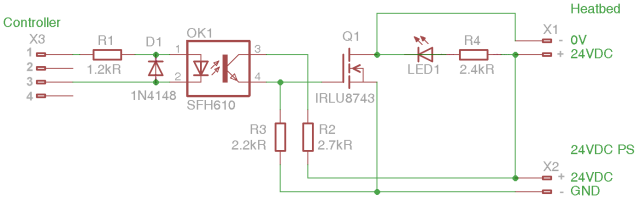
Als MOSFET habe ich den IRLU8743PBF
und als Optokoppler den SFH610A-1 verwendet.
(Beide bei Distrelec erhältlich: 60 54 21 MOSFET und 63 17 74 Optokoppler).
R4 und LED1 sind optional. Die LED leuchtet, wenn das Heizbett
eingeschaltet ist.
Bitte beim Nachbau die Pin Anordnung beim Optokoppler beachten:
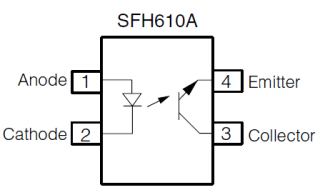 |
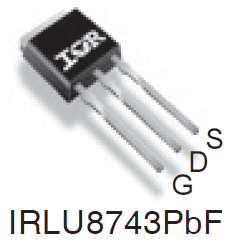 |
Anschluss der Schaltung:
X1: Anschluss Heizbett
X2: Anschluss 24VDC Netzteil. Polarität beachten!
X3: Anschluss an den Controller-Ausgang des Heizbetts (Pin 2 und 4 bleiben
leer)
Austausch des Hotends
Das bestehende Hotend funktioniert
soweit recht gut, hat aber dennoch einige Nachteile. Ich habe mich deshalb
entschlossen, das original Hotend durch ein Vollmetall-Hotend von
E3D auszuwechseln.
Folgende Verbesserungen sollten dadurch erreicht werden:
 | Einfacher Austausch der Düse. Das Original wird mit einer 0.5 mm
Düse geliefert. Beim E3D sind verschiedene Düsen ab 0.25 mm erhältlich.
Als Standard wird eine 0.4 mm Düse geliefert. |
 | Einfacherer Wechsel des Filaments: Bedingt durch die Konstruktion
des Velleman Hotends mit langer Teflon Röhre wird das Filament auf einer
langen Strecke warm und somit weich (teigig). Es klemmt dann im Hotend
und lässt sich teilweise nur schwer herausziehen. Das
E3D Hotend hat
einen scharfen Übergang vom kalten zum heissen Bereich. |
 | Bessere Druckqualität: Durch den scharfen Übergang vom kalten zum
heissen Bereich topft die Düse nicht, nachdem das Filament wenige
Millimeter zurückgezogen wird. Damit werden "Tropfen" und Unebenheiten
an den Seiten des Druckobjektes weitgehend vermieden.
|
 |
So sieht der neue Druckkopf (Hotend)
von E3D montiert am K8200 Drucker aus. Die Heizpatrone wurde ohne
Änderungen vom original Hotend übernommen.
Die Kunststoff-Aufnahme trägt
einen 40 x 40 mm Lüfter zur Kühlung und wurde vorgängig ausgedruckt
und natürlich vor dem Umbau auf Passgenauigkeit überprüft.
Die Montage erfolgt mit den Originalschrauben in den bestehenden
Gewindenlöchern.
Der Lüfter sollte immer in Betrieb sein, wenn das Hotend warm oder
heiss ist. Ich habe den Ventilator deshalb kurzerhand direkt an die
Stromversorgung des Druckers (15VDC) angeschlossen. Der Ventilator
läuft somit immer, sobald das Netzteil des Druckers eingeschaltet
ist. |
Wechselbares Druckbett mit BuildTak ®
Die von Velleman lieferbare
Glasplatte habe ich nun mit einer
BuildTak Folie
versehen. Damit haftet praktisch jedes Filament problemlos.
Die Glasplatte wird mit Klammern am Druckbett befestigt. Da ich mehrere
solche Glasplatten habe, kann nach erfolgtem Druck die Glasplatte einfach
abgenommen, eine leere Glasplatte befestigt und sofort weiter gedruckt
werden.
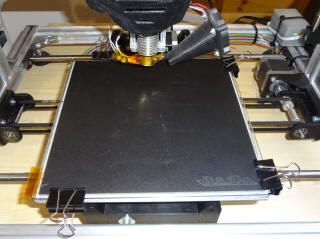 |
Auf diesem Druckbett hält alles:
Die mit BuildTak Folie beklebte, wechselbare Druckplatte.
Dank der Glasplatte ist das Druckbett absolut plan. |
Neuer Extruder und Hotend
Nach einigen Jahren Betrieb mit dem
K8200 und vielen vorgenommenen Verbesserungen habe ich mich entschlossen,
auch den Extruder und das Hotend zu wechseln. Das Hotend hatte ich bereits
gewechselt, und der Drucker hatte jahrelang ein E3D v4 Hotend, welches
wesentlich besser als das originale Hotend war.
Der Extruder war aber immer noch ein original Teil.
Das Problem dabei: Das Filament hatte keine durchgehende Führung. Somit
ergaben sich immer wieder Probleme beim Wechseln des Filaments - vor allem
dann, wenn es brach. Zudem ist es mit dem Original-Extruder nicht möglich,
flexibles Filement (z.B. Ninja-Flex) zu drucken. Flexibles Filament würde
sich einfach im Extruder ausbreiten und nicht durch die Hotend Düse
fliessen.
Das hat mich letztendlich dazu bewogen, mir den relativ neuen
E3D Extruder
"Titan" inklusive eines E3D v6 Hotends zuzulegen.
Schon vor einigen Monaten habe ich
deshalb einen E3D Titan Extruder mit neuem Hotend bestellt und erhalten.
Aber - da ich den 3D-Drucker regelmässig brauche - hatte ich die Umrüstung
bisher nicht vorgenommen.
Aber dann passierte es wieder einmal: das Filament brach innerhalb der
Extruder-Hotend Einheit. Nichts ging mehr. Ich hätte die gesamte Einheit
auseinander nehmen müssen, um die gebrochenen Stücke entfernen zu können.
Bei dieser Gelegenheit kann ich ja auch gleich die neue Extruder-Hotend
Einheit montieren!
Eine Montagevorrichtung hatte ich mir glücklicherweise schon vorher
konstruiert und ausgedruckt.
Also, los gings!
Der Schrittmotor musste
angeschlossen und die Drehrichtung kontrolliert werden (geht nur, wenn die
Temperatur des Hotends hoch genug ist).
Ein neuer Thermostat wurde montiert und angeschlossen. Die aktive Kühlung
mittels Ventilator wurde angeschlossen. Die Heizpatrone wurde dagegen vom
vorhergehenden Hotend übernommen.
Die zuvor ausgedruckte Montagevorrichtung wurde natürlich vorgängig auf
Passgenauigkeit überprüft.
Alles angeschlossen und getestet?
Dann kann es losgehen. Die Z-Achse musste neu justiert werden, da das neue
Hotend rund 15mm kürzer ist als das vorherige. Dabei wird der Druckbereich
natürlich auch um 15mm in der Höhe erweitert!
In der Firmware wurden noch die Extruder-Schritte von 600 auf 418 reduziert,
um dem neuen Extruder-Getriebe Rechnung zu tragen.
Und nun der erste Ausdruck:
Der erste Ausdruck war einfach nur perfekt!
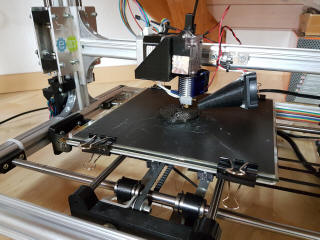 |
Der K8200 mit neuem E3D Titan Extruder
und E3D v6 Hotend. Sehr gute Ergebnisse!
Die Halterung kann als STL Datei auf der
Download-Seite heruntergeladen werden. |
Neues Druckbett
Das Original-Druckbett des K8200
ist eine einfache, geätzte Leiterplatte aus glasfaserverstärktem Epoxydharz
(FR3). Wie weiter oben beschrieben ist diese recht biegbar, und wölbt sich
zusätzlich im Betrieb, wenn das Druckbett erwärmt wird.
Bisher habe ich mich mit einer Glasscheibe beholfen, welche mit eine
Buildtak Folie beklebt und mit Klammern fixiert wurde (siehe Bild gleich
oberhalb).
Dadurch ist das Druckbett immer exakt plan und die Teile haften sehr gut.
Oder besser gesagt: Die Teile haften teilweise zu gut und lassen sich kaum
entfernen.
Die Firma Buildtak hat auch für
dieses Problem eine Lösung gefunden:
Das System nennt der Hersteller FlexPlate System und besteht aus drei
Teilen. Auf dem Druckbett wird eine dünne magnetische Platte fest verklebt.
Die Buildtak Folie wird nun auf einem dünnen, flexiblen Metallblech geklebt.
Dieses haftet jetzt magnetisch auf dem Druckbett und lässt sich einfach
wieder nach Druckende entfernen. Da das Blech flexibel ist, lassen sich die
gedruckten Teile ganz einfach durch leichtes Biegen des Bleches ablösen -
also genau was ich gesucht habe.
Leider tritt hierbei beim K8200 das
Problem mit dem gewölbtem Original-Druckbett wieder in Erscheinung, wenn ich
auf die Glasplatte verzichte.
Ein Möglichkeit wäre also folgende Anordnung gewesen:
 | Original-Druckbett (also die Leiterplatte) |
 | Glasplatte, mit Klammern befestigt oder fest verklebt |
 | Buildtak magnetische Basisplatte auf die Glasplatte geklebt |
 | Buildtak FlexPlate |
 | Buildtak Folie auf das FlexPlate geklebt |
Das waren mir aber doch zu viele
Schichten, was zu instabil und gebastelt und zudem dem Wärmefluss nicht
gerade zuträglich gewesen wäre. Ich habe mich deshalb entschieden, das
Druckbett auszutauschen.
Ein geeigneter Ersatz ist das MK2B-Aluminium Druckbett, wie es für RepRap
Drucker angeboten wird. Dieses kann an 12V oder 24V Systeme angeschlossen
werden. Ich hatte ja die Heizung schon früher auf 24V umgebaut, elektrisch
passt es also.
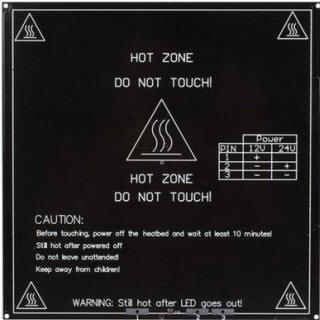 |
So sieht das neue Druckbett aus. Es besteht aus rund 4mm
dickem Aluminium Blech und kann an 12V und 24V Systeme angeschlossen
werden.
Im kleinen Loch in der Mitte wird der Thermostat von unten
eingeklebt. |
Der Umbau ist recht einfach: Das
Original-Druckbett wird abgeschraubt und die Litzen für Heizung und
Thermostat abgelötet. Für die Befestigung des MK2B müssen neue
Befestigungslöcher in der Alu-Trägerplatte des K8200 gebohrt werden. Mittig
wird zudem ein weiteres Loch (ca. 8mm) für den neuen Thermostaten benötigt.
Der mitgelieferte Thermostat des MK2B hat wie beim K8200 einen
Widerstandswert von 100kOhm und wird von unten eingeklebt (Epoxy Kleber).
Die Litzen für die Heizung und des Thermostaten werden am MK2B angelötet,
wobei die Thermostat Litzen verlängert werden müssen. Anschliessend wird die
ganze Einheit am K8200 verschraubt.
Nach erfolgreichem Test des neuen
Heizbettes wird die Buildtak Basisplatte auf den MK2B geklebt.
Die Buildtak Kunststoff-Folie wird auf das FlexPlate geklebt und zusammen
auf der Basisplatte positioniert.
Die Z-Achse muss nun neu justiert werden, danach kann mit dem ersten
Testdruck begonnen werden.
Bei mir hat der erste Druck perfekt funktioniert.
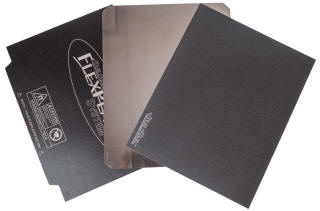
Bild: Buildtak |
Aus diesen Komponenten besteht das Buildtak FlexSystem:
- Die magnetische Basisplatte (links), welche auf dem Druckbett fest
verklebt wird
- Das FlexPlate (mitte), ein dünnes Metallblech
- Die Buildtak Folie (rechts), welche auf die FlexPlate geklebt wird |
Dieser Umbau ist sehr
empfehlenswert. Gegenüber dem K8200 im Originalzustand ergeben sich folgende
Vorteile:
 | Grosse Heizleistung für schnelles Aufheizen und höhere Temperaturen. |
 | Absolut plane Oberfläche des Druckbettes. |
 | Die meisten Filamente haften ohne weitere Massnahmen gut. |
 | Einfaches Ablösen der fertigen Teile. |
 | Die FlexPlate wird auch einzeln angeboten. Man kann also mit
mehreren Folien arbeiten, beispielsweise zum schnellen Wechseln, oder
mit anderen Folienfarben und sogar anderes Folienmaterial (BuildTak PEI
Folien). |
 | Keine Klammern notwendig, da magnetische Haftung. Dadurch keine
Gefahr, dass der Druckkopf in die Klammern prallt oder die Klammern sich
am Drucker verhaken. |
Fazit
Im grossen
und ganzen ist dieser Drucker absolut zu gebrauchen. Feineinstellungen und
eigene Optimierungen sind
aber notwendig für ein gutes Ergebnis. Das
Velleman Forum für diesen Drucker ist voll von Ideen und
Verbesserungsvorschlägen, welche zum Teil auch sehr einfach umzusetzen sind.
Das schöne daran ist, dass im Forum sehr viele begeisterte Anwender mit viel
Erfahrung vertreten sind, welche die selbst konstruierten Teile zum Download
bereitstellen oder bei Fragen gerne behilflich sind. |